We often remodel gold engagement rings, and platinum too for that matter.
Meeting the Metal Challenge
Can you create a brand new engagement ring by melting the metal from your existing one? Or any piece of jewellery for that matter?
I’m regularly asked this question, and the shorter answer may include, “yes, no, if you don’t mind spending more money”. I know that's ambiguous. Sorry, it's down to what you are looking for.
Note to the guilty
If this is an engagement ring, I know for most women at this situation, this isn’t a decision that was taken lightly. As soon as that engagement ring is slipped on your ring finger, it is more than just a piece of jewellery, it is a treasured keepsake. However, to enjoy wearing it every day, ideally it needs to suit your hands and your lifestyle. If it is jarring you, then it probably isn't. You may have found this blog post conversation with your fiancé/husband - if not, and it is your engagement ring, you probably should.. ;-).
Reusing Rings to Make Rings
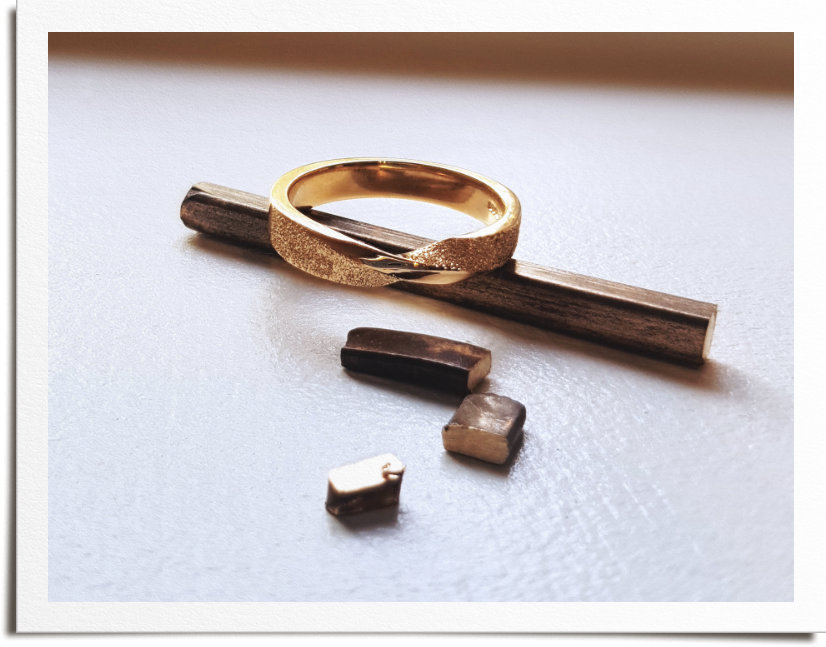
Handmaking
Handmaking jewellery is the most flexible way to ensure you can keep at least some of your original metal as it is usually possible to reuse the old jewellery;
- If the issue is just that you don't like the stone collet and want to change this - it's a straightforward job. We aren't doing any major changes to the shank, we can cut back into it and prep it up for a new collet (provided they are compatible) no problem.
- If you want to increase the shank thickness or depth, or add/remove diamonds we can still do this, adding more metal to the metal you have and drawing it back into wire, to reshape into a ring. You are going to lose a bit of metal from this because melting, cutting and polishing and invest in a bit more, but making up plain and gem set ring shanks is fairly straightforward once the gold has been reprocessed.
- The same here applies to platinum. So anywhere where the jewellery you want is possible to hand make, it is possible to reuse your gold or platinum.
Costs of hand-making jewellery
Depending on where you go, it is possible to have jewellery remade quite cheaply by jobbing goldsmiths. There may be no guarantees or promises (and you really need to be careful that you are going to somebody who is trustworthy as there are a lot of questionable practices out there) but if your perception is that it shouldn't cost more than £100 to remake a ring, this is going to be your best option.
At the other end, is what goes into the project. Time and labour, expertise, material accessibility and availability. A good goldsmith has a deep understanding of jewellery making techniques from different eras. They will advocate for and against different approaches depending on the piece and the wear levels. Expect things to start from a few hundred pounds to remake a ring.
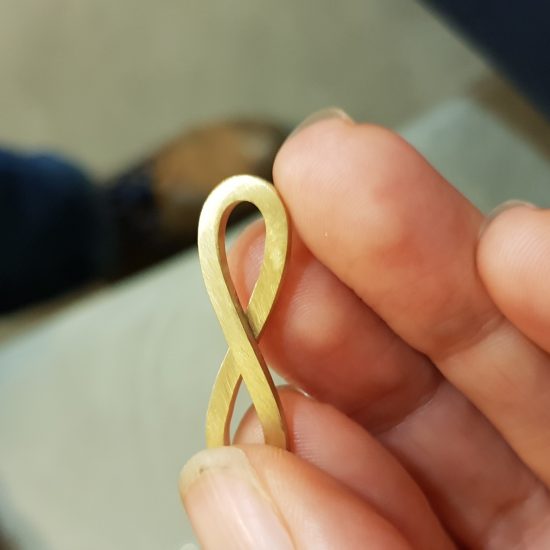
We have and do melt down old jewellery and incorporate it into new pieces. See our case study where we remodelled an old gold wedding ring into an infinity symbol. The infinity symbol is made entirely from the old gold wedding ring.
Melting Old Jewellery
Where more detail is required on an item of jewellery, and it can’t be made by hand is where challenges start. Casting jewellery is where hot metal is forced into a hot mould. It is the most common process for jewellery making today. This is because a lot of pieces can be made at once, making it very cost effective.
Casting involves more metal than will be in the final design. Rather than explaining it all here I suggest you watch a video I had made on the engagement ring production process.
Cast pieces always require to be ‘cleaned up’. To melt a gold ring down and cast a new piece, would still require additional metal for the mould. Casting is a highly controlled process, and the metals and compositions of are carefully controlled. Your ring in this case would be considered a pollutant. Metal which the client would have to pay for, because it would not be usable elsewhere once combined with their jewellery.
Smaller Scale Casting
It is sometimes possible, using more traditional casting methods to produce simple pieces using simple moulds. But they do have to be SIMPLE. Cast jewellery production involves keeping everything as hot as possible to delay the metal solidifying and leaving parts missing. In a workshop, there is not the scale to work this way. However, once things are becoming more simple again, handmaking is often the winning approach.
Keeping the jewellery involved
A way that we work around utilising old pieces in new designs is to combine techniques. So, a complex stone setting may be cast, but the original shank is reused in the new ring shank, as this is straightforward to do by hand.
The most cost-effective options for ring remodelling
Lets consider this ring:
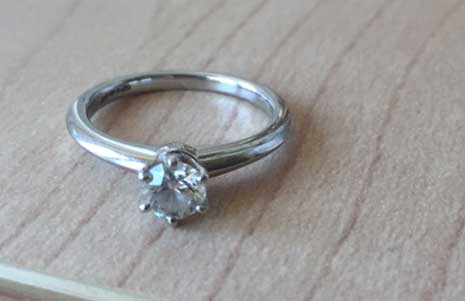
1. Keep the stone setting
Sometimes, it is a simple tweak that will change the ring. In this example, the stone is felt to be a little stark against the shoulders of the ring.
The client is very attached to the ring, and wanted as much of it as possible to be involved in the creation of a new ring. She liked the sparkle of diamond shoulders. The shape of this ring would mean it wouldn’t be possible to set diamonds in the band itself (it is called an ‘apex’ or sometimes ‘knife edge’ band because the profile tapers to a soft edge), but we could keep the stone setting. It would come out looking a bit like this;
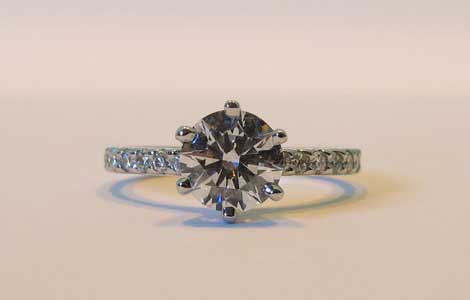
2. Keep the shank
An alternative option, would be keeping the actual ring band itself (called the shank) and setting the stone in a new mount. The first ring pictured has a good solid shanks we can reshape and rework, and combine with the collet style desired.
3. Recycle the shank and setting
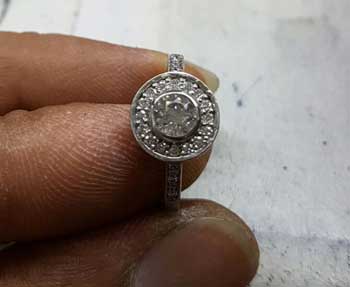
The final option is to recycle the existing shank, and use the payment for this towards a brand new ring setting, retaining the diamond of course.
If requested, part of the original ring could still be incorporated, perhaps a tiny section being melted and added to the ring profile as small beads of metal. In some cases, we can still add a little metal to the new shank.
The majority of our clients choose a brand new ring design for their existing stones. They have to balance between costs, sentiment and style. However if the engagement ring owner is comfortable her fiance approves, she’s most keen to create a ring style which works for her.
The cost factor
For the majority of our customers, the desire is to manage the cost of remodelling an engagement ring. This is because their fiances are likely to have already invested in the original ring. This is what deters them from melting a ring down.
So it is better news that as we’ve seen, potentially there are ways to save parts of the original band, and still create something fresh and new. The best option from a financial perspective is to recycle the gold (or indeed platinum) from the existing ring, and use the income from this to create the ideal design.
Get in touch with your ring requirements.
A little education;
Why Melting Different Metals together can be problematic
Take a hypothetical 18 karat gold ring. 18 karats is 75% pure gold, and 25% additional metals which help with ensuring the gold is durable enough for everyday wear. We call this an alloy. Gold is the primary element, but we don’t know what the additional ingredients are. There are literally thousands of gold alloys in existence. Even going back to the same company who made the ring in the first instance doesn’t mean they are still using the same alloy. And alloys don't always get along. Combining two may soften the metal, or cause cracking. You probably don't know if the ring has been made from other rings which have already been melted down.!
I could get even more technical, but I think I’ll leave the case here – melting a gold ring may weaken the metal, or change it slightly.